Fabrication automobile – Giga-casting, giga-dépenses pour les automobilistes
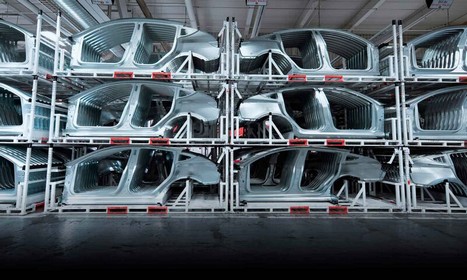
Inauguré par Tesla pour la fabrication du Model Y, le giga-casting consiste à remplacer plusieurs pièces de châssis assemblées par soudage par un seul gros élément moulé. Avantageuse pour le constructeur, cette solution peut se révéler coûteuse pour les automobilistes en cas de réparation. Explications.
Nouvelle technique de fabrication pour certains éléments des châssis de voitures, le giga-casting permet l’utilisation d’énormes presses de moulage sous très haute pression pour créer des pièces automobiles d’un seul bloc, éliminant les étapes d’assemblage traditionnelles. L’idée peut sembler séduisante, mais seuls les constructeurs automobiles pourraient en tirer profit. La Feda (Fédération de la distribution automobile) alerte le public : « Sous couvert d’innovation, de simplification du montage et de gains de compétitivité, cette pratique est d’abord synonyme d’amélioration des marges pour les constructeurs. Elle comporte aussi d’importants effets pervers, tant sur le plan environnemental que pour les consommateurs. »
Des avantages… pour les constructeurs
Pour une même fonction, les chiffres montrent que le giga-casting permet de réduire le poids des pièces jusqu’à 30 % tout en offrant une solidité similaire à celle des pièces remplacées. Ainsi, le châssis du Model Y de Tesla est 40 % plus léger grâce à cette technologie, ce qui promet une meilleure efficacité énergétique de la voiture. Grâce au giga-casting, la partie arrière se compose aujourd’hui de deux pièces et n’en comportera bientôt qu’une seule. En comparaison, la même zone d’un Model 3 est constituée de 70 pièces. Outre la réduction drastique du nombre d’éléments, il semblerait également que le résultat offre une meilleure résistance aux chocs, donc apporterait plus de sécurité pour les occupants. Enfin, la réduction des coûts de production peut atteindre les 20 %. En effet, l’utilisation de la giga-presse d’Idra (le fabricant italien fournisseur de Tesla) remplace environ 60 robots traditionnels.
General Motors utilise aussi cette technologie pour sa berline électrifiée, la Cadillac Celestiq, tout comme la marque chinoise Zeekr pour son SUV 009. D’autres constructeurs vont prochainement leur emboîter le pas (Toyota et Hyundai notamment). Certains constructeurs passent d’ores et déjà par une étape intermédiaire, le méga-casting, où les pièces fabriquées sont un peu moins importantes qu’avec le giga-casting. C’est le cas de Volvo qui a annoncé investir environ 1 milliard d’euros dans son usine de Torslanda (Suède) pour la production de voitures électriques de nouvelle génération où les principales parties de la structure du plancher de la voiture seront désormais fabriquées en une seule pièce. Et de confirmer que « la méga-presse présente l’avantage de simplifier le processus de production, ce qui engendre à son tour des économies de matériaux et de logistique ».
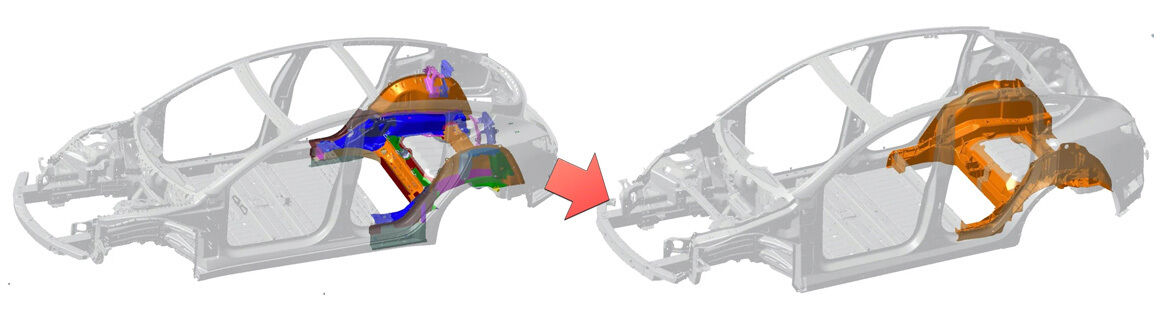
Des surcoûts pour les automobilistes
Si les constructeurs voient le méga-casting d’un bon œil, et a fortiori le giga-casting, on peut légitimement craindre des effets pervers, pour les automobilistes comme pour l’environnement.
Le premier concerne le budget des ménages qui risque d’en prendre un coup avec des réparations bien plus coûteuses. En effet, le coût du remplacement d’une « méga-pièce » au lieu du changement, voire de la réparation d’un petit élément sera bien plus important. La Feda estime par exemple que la réparation d’un choc arrière très important sur une Peugeot 2008 coûte actuellement 12 154 € pour 6,5 jours de travail. En simulant une conception par méga-casting, cette même intervention serait facturée 15 402 € et demanderait 11 jours de travail. Ce serait encore plus onéreux en cas de giga-casting. Pire encore, la réparation pourrait même être remise en cause dans le cas de véhicules très endommagés dont la valeur serait inférieure au coût de la réparation.
Le second écueil concerne les effets néfastes du giga-casting sur l’environnement. En effet, le remplacement d’une seule grosse pièce est moins vertueux en termes de fabrication et de transport que celui d’un petit élément. Sans compter qu’il serait préférable de réparer cette petite pièce plutôt que de la remplacer. En outre, la production de ces pièces de grande taille nécessite bien plus de matière première et d’énergie.